A house with no nails
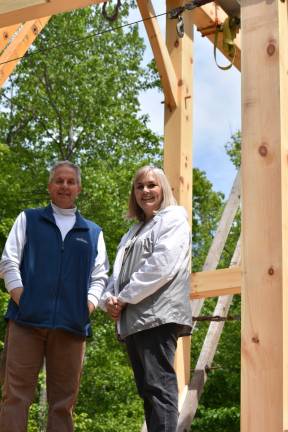
On their 39th anniversary, watching the giant beams go up
By Becca Tucker
The timber frame rising from the ground is a common enough sight in rural Sussex, NJ. But this is no hay barn. It’s a 2,300 square-foot post and beam home, one that Sheree and Jim Vogt expect to hand down to their grandchildren’s children.
Their wooded seven-acre property backs up to over 1,000 acres of state-owned wildlife preserve. The piece of land has been in Jim Vogt’s family for four decades. In New Jersey, the most densely populated state in the country, “here we are without a single soul around. It’s a very privileged opportunity for us, very humbling actually,” said Jim. The couple has been renting a condo in Newton, NJ, waiting patiently for this moment. The day they watch their frame go up happens to be their 39-year anniversary. Tonight they’ll go out to dinner, it doesn’t matter where.
“This morning there wasn’t anything vertical,” said Jim, as we watch the five-man crew prepare to raise the second of the house’s four enormous upright sections with a crane.
The construction crew, Wood Structures, happens to be out of Branchville, NJ, but they are a specialized timber framing team that travels as far as Colorado for a build. They’re led by Mike Moore, who wears suspenders over his t-shirt and a baseball cap over his bushy white hair. Moore built his first timber frame home 1975 and is still clambering around the high beams 20 feet up, catching a mallet tossed up to him with one hand.
“He fits the mold of these timber framers to a T,” said Jim, watching from below. “Just very old school, very approachable, very knowledgeable and passionate about this type of construction. You rarely see very young people” go into this specialized line of work, he said.
Mortise and tenon construction–which uses wooden pegs instead of nails–goes back thousands of years, to seventh-century Buddhist temples in Japan. (The cathedral of Notre-Dame is one example that’s been in the news recently.) The ancient art of framing a house with huge beams, mallets and pegs is having a minor revival, but it’s still rare in the U.S., accounting for a fraction of a percent of new homes. Typically seen in Amish or Bruderhof communities, it’s a relatively high-end option in the mainstream world. A timber frame home costs 15 to 20 percent more than its stick-built counterpart, but it’s also 20 to 30 percent more energy efficient.
“Every time you have a stud,” a two-by-four against an outside wall, “that’s a poor insulation material,” explains Jim. A timber frame house, on the other hand, has no studs or structural interior walls. The spaces between the posts and beams will be fitted with blown insulation called structural insulated panels, or SIPS. “Like a coffee cup, almost,” said Jim.
When you step into the house, you’ll enter an open space. This will be the great room-slash-dining room-slash-living room-slash-kitchen. Sheree will have a lofted art studio. There will be a full basement with a bathroom for grandkid visits.
And because the house is prefabricated, it goes up fast. “They’ll have this house up and ready to enclose… once the process starts it usually takes about a week,” Jim said. Piles of Eastern white pine, harvested and processed in New Hampshire, sit under tarps, pre-cut to fit snugly into one another and labelled with permanent marker. “It’s almost like putting together a jigsaw puzzle,” said Jim. There will be next to no construction waste, another advantage over stick-built construction.
When it comes to construction methods, it’s safe to assume the couple has done their homework. Jim is a representative for the company that designed the frame, Davis Frame, and also works for Loew’s pro services department, which supplies materials to builders. Sheree works in marketing at a concrete company called CST Pavers.
“Families hand these things down from generation to generation,” said Jim. “When you think about resale value for something this unique? It’s a powerful equation. This is definitely not mainstream construction.”
Cost: $250,000-$300,000